Making the most of a small shop – PART 6
Up to this point (Part 1 – 5), I have managed to install the bulk of my larger tools into my All-In-One Woodworking Workstation with the exception of my thickness planer.
Installations already included:
- Table saw – PART 2
- Miter saw – PART 3
- Workbench with vice and power tool storage – PART 4
- Soundproof compressor enclosure – PART 5
Installations to be added:
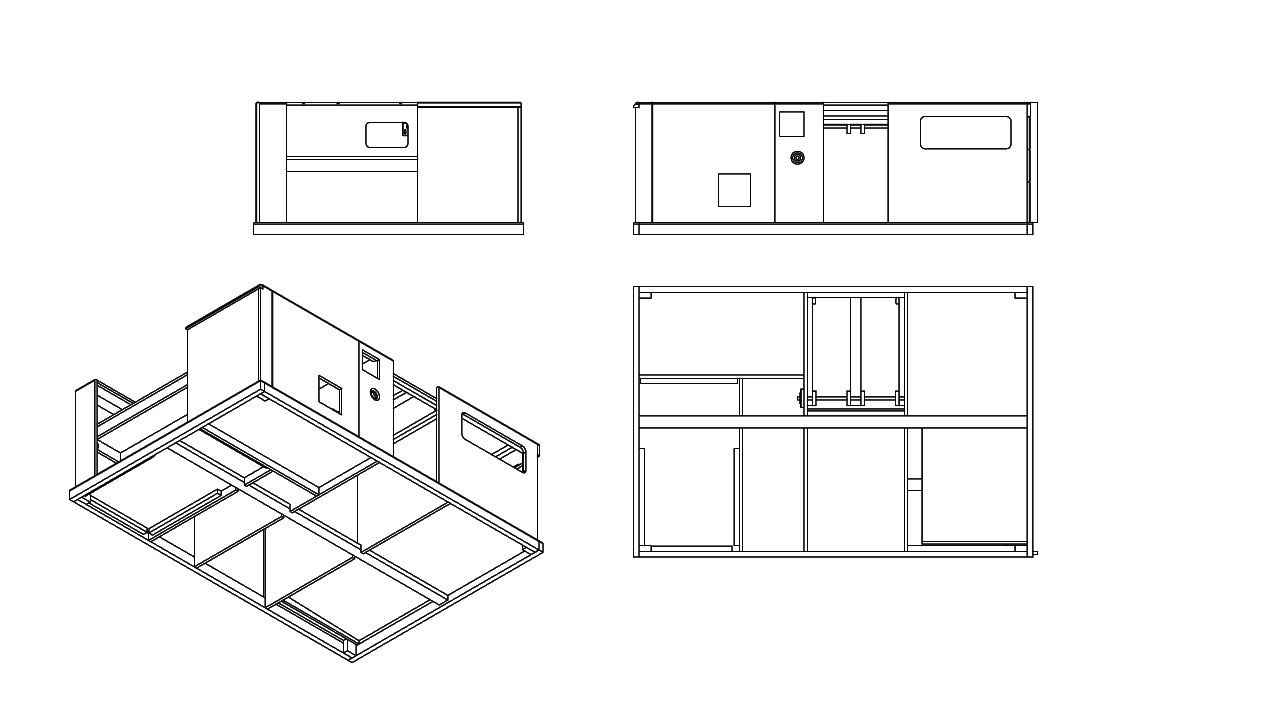
>>>GET COMPLETE PLAN<<<
Rotate-To-Store Flip Top Thickness Planer
Adding my 318mm(13inch) thickness planer to the bench was the next logical step because it is a piece of equipment that I find myself using often. It is also a tool that performs better with extended infeed and outfeed tables to limit or even eliminate planer snipe.
It is, for this reason, I decided on placing it more toward the center of the bench and across from the already installed miter saw. This would place it right in the firing line of the table saw so it would need to be able to fold away to prevent the two tools from clashing.
In addition, to maximize the infeed and outfeed support capability of such a large bench the planer needed to be recessed to get the planer bed flush with the bench top.
PART 6: Flip-top thickness planer
The instructions that follow are intended to be considered along with the video instructions provided above.
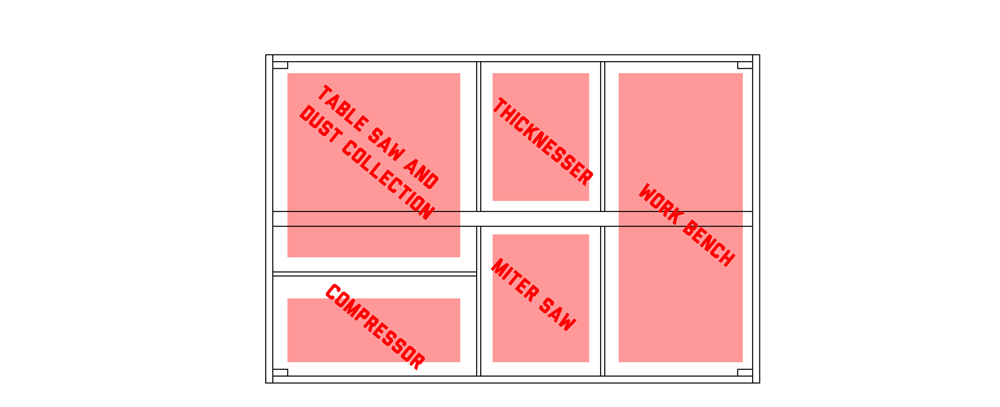
Step 1: Top cutout
My first step in adding my thickness planer to my workstation was removing the segment of the top where the planer would be installed.
Like in Part 2 and Part 3, guide planks were installed on the underside of the bench top to represent the borders of the cutout. A jigsaw was then used to remove the bulk of the unwanted segment by cutting slightly (5mm or 1/4″) toward the inside of the guide plank.
After doing this I was able to run my router with a flush trim bit along the inside of the guide planks to create a clean, straight edge around the border of the cavity.
Step 2: Planer base
The rotating planer bed was assembled next.
The rotating bed was assembled with a 19mm(3/4″) thick wall stainless steel pipe in the center to act as a pivot point and allowing it to make a 180° rotation for packing away the planer.
The pipe was then sandwiched between an arrangement of planks (diagram 1 and 2) that was slightly thicker than the pipe diameter. This was done to minimize any deflection in the pipe while still allowing the pipe to move freely.
This arrangement of planks also formed the base on top of which the planer was going to be fixed (diagram 2). The rest of the bed was then assembled as a box around the base.
The depth of the base (for fixing the planer) relative to the top of the box needed to be the exact height of the bed on the planer itself so that when the planer is fixed to the rotating base the planer bed would line up with the top of the box.
The distance from the center of the shaft to the top of the box needed to be matched toward the underside of the box (i.e. the pipe needed to be installed in the exact center between the top and bottom of the box).
This was important because the tool/planer needed to sit flush with the bench top. When the tool is in its stored position the underside of the box (which would then be at the top) needed to complete the removed segment of the bench top.
The final panel (diagram 4) on the rotating bed was only installed after fitting the planer to the bed so that bolts could be used to fix the thickness planer to the base panel.
This would be done after fitting the bed to the workbench in the next step.
Step 3: Fitting base to the bench
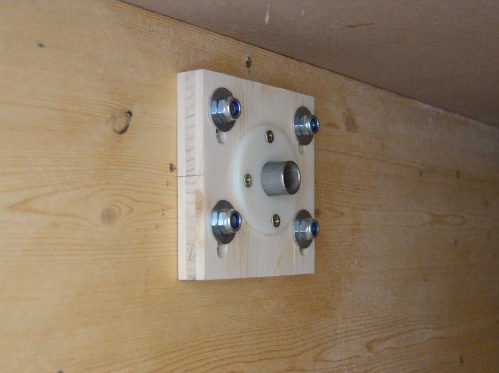
The rotating bed was installed to the All-In-One Workbench in the same way as the fold-down miter saw base in Part 3. By mounting height adjustable bushings on the two partitioning panels that form the sides of the cavity. Then running the pivot shaft of the rotating bed through these bushings.
However, instead of placing the bushings at the rear of the bed to allow it to fold down (such as in the case with the miter saw bed), the bushings were mounted in the center to allow the bed to make a 180° rotation.
The bushings were installed over slots that were cut into the partitioning panels to allow the shaft to move up and down when adjusting the height of the bush housing. This allowed for the rotating bed to be perfectly aligned with the bench top.
The bush housing was then secured by tightening the bolts and the planer was mounted to its base using bolts through the base panel.
After the planer was secured the final panel (as shown on step 2 diagram 4) was fixed in place.
Step 4:
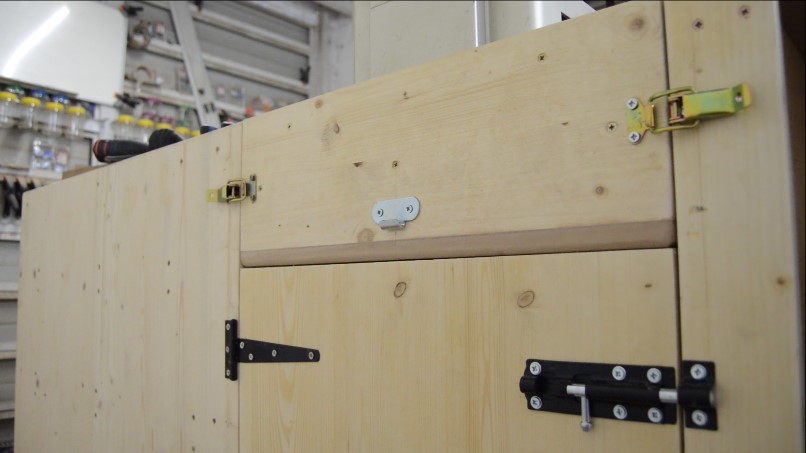
The final step in this installation was adding toggle latches to secure the planer bed in either its working or stored position.
A door was also added to the opening under the rotating bed.
Because the shaft was in the center of the rotating bed the weight was well balanced and little force was required to keep the bed in a level position.
Part 6 finished!
Installing my planer on a rotating bed was a great idea. When it is not being used it is stored upside down and out of the way while the box completed the bench top to provide a larger working surface.
To use the planer I would open the door, disengage the latches, and swing the planer over into its working position before re-engaging the latches to secure the bed.
Because the planer bed was installed flush with the bench top I saw a great reduction in planer snipe.
Now that all that’s left to add to the bench is my shop vac and router, the bench is nearing completion.
Wonderful and interesting site. Rational advice on the use and placement of the necessary equipment. Your knowledge and experience in this topic is impressive. Thanks.
I’m in the process of building one of these myself, and it’s coming along reasonable well. Would you happen to have a link or a description to the three toggle switches you’ve used to secure the planer bed? I’m having a hard time sourcing these.
Sure thing. Here you go. https://amzn.to/2xiqbMy
Where can I find the aluminium locks you used the keep the stainless steel rod in place? If they are not available, can you suggest an alternative?
I made the ones in the video myself. A simple alternative would be a cotter pin.
Hello, can you please let me know where I can find the aluminium end caps you used the pinch the stainless steel rod? If not, can you recommend an alternative?
Hello, can you please give me the mesure of your workstation , because i’m pretty sure its not a 4’X8′(4feet by 8feet) it look a lot huge tanks its so cool to see you working
Awesome work, I really enjoy your videos. I am Currently building a similar work bench and adding the flip top planer. Could you tell me where you got the bushings for the housing? I can’t find them anywhere.