Carbide tip saw blades
Odds are, when buying a new saw, whether table, circular or miter, it often comes fitted with a mediocre blade.
While these types of blades are often all-rounders and are more than good enough to produce most cuts well enough, in some cases the woodworker may want to opt for a blade better suited to a specific task.
In this articles we will be looking at all the different components of carbide tipped saw blades and how they relate to the quality of your cuts.
Choosing a table saw blade or even a blade for your miter or circular saw becomes much clearer when armed with the correct information
Factors to consider when choosing a new saw blade:
- Saw – Different saws operate better with different blades. An example would be a miter saw. As these saws are intended for crosscuts they would perform their best when fitted with a blade intended specifically for crosscuts.
- Type of cuts – While some blades perform better when ripping others are designed for crosscuts. Some can handle a faster feed rate and some require a slower feed while others can rip clean enough for gluing without running through a jointer.
Are you looking for an all rounder or do you want to build a stock of cut specific blades? - Material or stock being cut – Consider what the blade will be used for as different materials require different blades. Some materials, like laminates, tend to produce more chip-out. In these cases, a blade better suited to the material should be used.
Blade anatomy
Tungsten carbide tip (TCT) – The business end of the blade. These are arranged around the circumference of the blade and are made from a much harder material (tungsten) than the rest of the blade, giving the blade a longer useable lifetime.
Due to the hardness of these tips, they will not warp or bend when they are subject to a mechanical stress but would rather break. It is for this reason why any embedded metals in a stock like nails or screws can and will destroy a blade if the blade had to come in contact with it while cutting.
Gullet – This is the name given to the area in front of each tooth. The gullet is to make space for the wood shavings that come of the stock when sawing. Generally, the closer the TCT’s are together the smaller the gullets are as the tips shave off less with each pass.
Sawteeth – These are the areas protruding between gullets that house the TCT’s. Smaller gullets allow for more teeth which are common on crosscut blades.
Stress reliever – These slots are to accommodate heat build up within the blade to prevent the blade from warping or buckling.
When cutting denser materials like hardwoods, a blade can generate a good deal of heat build up within the blade. This heat will cause the blade to expand. The expansion will be accommodated by the areas removed that form the expansion slots or stress relievers.
Hook angle – The hook angle refers to the pitch of the tip with respect to the center of the blade. Either forward (positive) or backward (negative). A larger or more positive pitch would produce a faster, more aggressive cut which is better suited to ripping while crosscut blades have a lower or negative pitch to restrict feed rate. Most standard blades possess a positive hook angle of between 5 to 15 degrees.
Kerf – The kerf refers to the area of wood removed after cutting and the kerf width is determined by the width of the TCT.
Blades are available in thin kerf (<1.8″) and full kerf versions with thin kerf blades being more intended for lower powered saws. The thin kerf blades receive less resistance from the stock as a smaller area is in contact with the stock when sawing but they tend to be more unstable as then can bend more easily.
Types of blades
There are many different types of saw blades that are determined by their tip configuration or “grinds” of which the four most common ones are: Flat top grind (FTG), Combination (ATBR), Alternate top bevel (ATB) and triple chip grind (TCG).
1. Flat top grind – Are square tipped (raker) tooth blade for fast and aggressive ripping where chip-out is not a concern. They are most durable and long lasting while being easier to maintain.
An FTG blade cuts through the stock by removing small squares with each tooth pass and so creates a fair amount of splintering.
2. Alternating top bevel – These are of the more common type of blades. They are made with beveled tips arranged in a crisscross pattern. Adding a pitch such as this to the tip of the blade makes for a smaller amount of the tip doing the cutting and so generates less chip-out with the largest drawback of having a blade that dulls faster.
In the case of woods that tend to generate high amounts of chip-out like pressboard or veneered woods, an HI-ATB blade does a better job.
3. Combination blades – These are blades that possess a combination of the above-mentioned tip arrangements. Combinations blades are considered general purpose blades as they possess a crosscut component but also a ripping component.
Tips are normally arranged in a four-to-one fashion with four ATB tips followed by one FTG tip.
Triple chip grind – These configurations are more intended for harder materials like plastics, metals or laminates.
These blades are made to be more resilient while also limiting chip-out in harder, more brittle materials.
.
Blade sizes
Tungsten carbide tip blades come in various sizes from 4-1/2″ to 12″ while 10″ is generally the go-to blade size for most hobbyists type table saws.
Miter saws normally use 7 or 10″ blades while circular saws can be made to operate with blades as small as 4-1/2″.
Teeth count
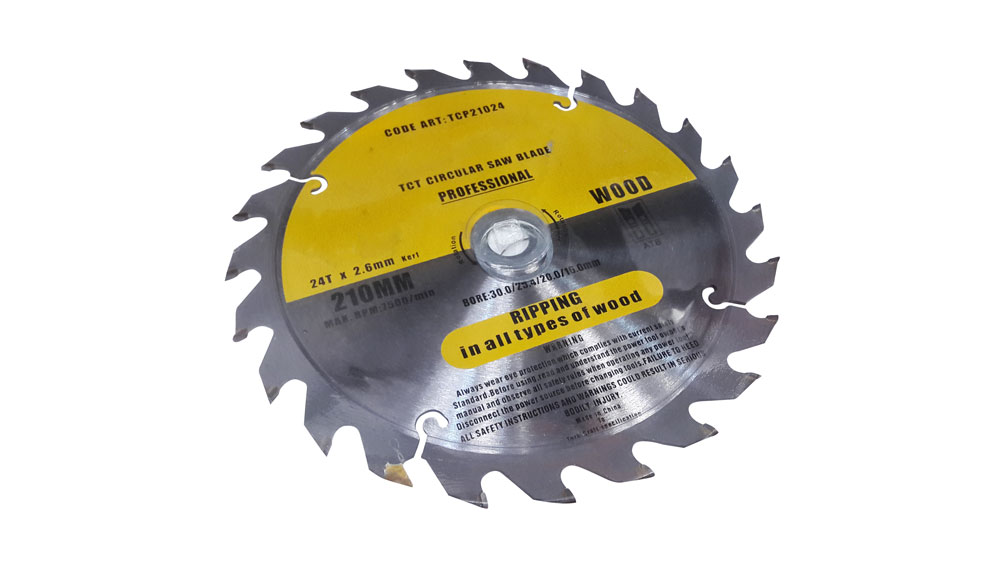

The teeth count of a blade is one of the more prominent factors that will determine the quality of a cut.
More teeth generally mean cleaner cuts while being indirectly proportional to feed rate. The reason for this is smaller gullets.
For the blade to accommodate more teeth the gullets need to be decreased in size and so allowing less space for wood being shaved from the stock.
60 teeth and up are more often used for crosscutting. They produce very little chip-out while requiring a slower feed rate.
In the cases where cleaner cuts are not essential, a blade with a lower tooth count will work just as well while costing less and also cutting faster.
Hey, Jean. A few months ago I purchased a small cheap saw to cut the cheap wood (LOL) I was using to make a temporary fence to divide my side yard so my dog couldn’t get to my plants which are on the “forbidden” side. I obviously wasn’t aware that saws come in a variety of blades and had a tough time cutting the wood. I figured they were all the same and it was just a matter of how sharp it was. This is really good information. Thank you for sharing!
Hey Cindy,
Yes, the blade does indeed make a big difference if you are looking for the absolute best cut but for general duty around the house, a good quality standard blade or combination blade will be more than good enough.
Glad you found the post useful. Stop by soon.
Jean
A great piece of information. I think this is what I was exactly looking for. All tips in a single click. I would definitely try to follow these suggestions. I really enjoyed this post and I hope you will keep posting this kind of post in future.
Hey Steav,
I will indeed.
Thanks for stopping by.
Jean